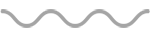
Latvian and international standard regulating hot dip galvanized coatings on fabricated iron and steel articles is LVS ISO 1461
Requirements of the standard are not mandatory yet they can be applied at the customer’s choice.
Prior to accepting the article for treatment galvanizer shall know whether it is necessary to galvanize in compliance with this standard.
What does the standard regulate?
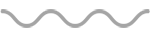
Definition
Hot-dip galvanizing is a formation of zinc coating and (or) zinc-iron alloy on steel (cast iron) products, by immersing product of steel (cast iron) in molten zinc.
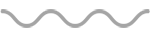
Thickness of the Zinc Coating
Coating minimum thicknesses on samples that are not centrifuged:
Article and its thickness | Minimum local coating thickness(μm) | Minimum mean coating thickness(μm) |
Steel > 6 mm | 70 | 85 |
Steel > 3 mm ≤ 6 мм | 55 | 70 |
Steel ≥ 1,5 mm ≤ 3 мм | 45 | 55 |
Steel < 1,5 mm | 35 | 45 |
Cast iron ≥ 6 mm | 70 | 80 |
Cast iron < 6 mm | 60 | 70 |
Coating minimum thickness on centrifuged samples:
Article and its thickness (mm) | Minimum local coating thickness(μm) | Minimum mean coating thickness(μm) |
Article with threads: | ||
≥ 20 mm | 45 | 55 |
≥ 6 < 20 mm | 35 | 45 |
< 6 mm | 20 | 25 |
Other articles (incl. castings) | ||
≥ 3 mm | 35 | 55 |
< 3 mm | 45 | 45 |
Zinc Quality used for Galvanizing
Galvanizer shall control that zinc used for galvanizing complies with requirements of EN 1179 and contains not more than 1.5% admixture, with exception of iron and tin.
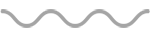
Test Procedure
Test may be by electromagnetic method, measuring coating thickness in microns, or chemical test determining weight of coating. To obtain precise results of the coating thickness measurement shall be made on all surfaces.
Number of measurements to be made:
Area of product surface (m²) | Number of places to be measured | Number of measurements in each place |
≥ 2 m² | 3 | 5 |
≥ 0,01 m² < 2 m² | 1 | 5 |
≥ 0,001 m² < 0,01 m² | 1 | 5 |
< 0,001 m² | 1 | 5 |
Number of test articles for which test analysis of coating thickness should be performed depending on the number of articles in the lot. If the articles are of different shape and size and total number of articles to be galvanized is small, you can demand to test all of the articles. The abovementioned instructions mostly refer to large amount of small articles, such as nuts, bolts, fixings and the like.
Number of articles in the lot | Number of articles in the test sample |
1 - 3 | All |
4 - 500 | 3 |
501 - 1200 | 5 |
1201 - 3200 | 8 |
3201 - 10000 | 13 |
More 10000 | 20 |
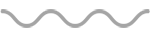
Appearance of the Zinc Coating
Visual inspection should not detect cavities, roughness, and sharp points. There should not be blisters (uncovered areas) and ashes. Some articles are hard to galvanize so that to obtain smooth, even surface. Insignificant amount of slag or zinc leakage may be left in the corners, yet in case of such, they may not be in places that hinder or make the usage of the article impossible.
Point 6.1 of the standard provides that dark or light spots, or slight roughness of surface, is not a reason for rejection, as well as dark spots from storage in humidity (“white” or “dark” rust – zinc oxides formed on hot-dip galvanized surfaces stored in humid circumstances) is not a reason for rejection as long as the thickness of zinc coating is of the required minimum thickness specified in the standard. Colour of zinc coating is formed within two months depending on the composition of different chemical elements in the steel to be galvanized and their placement in the surface of this steel. Galvanizer cannot influence the colour of coating. Regardless of the different colour of zinc coating, its anticorrosion characteristics is unchanging.
Renovation of Uncoated Areas
Even the best galvanizing treatment may sometimes require correction of some small size uncoated surface area. Most often the reason for non-formation of the coating is the presence of specific substances on the surface of the steel that cannot be removed by hydrochloric acid.
The total uncoated areas for renovation by the galvanizer shall not exceed 0,5% of the total surface area of an article. Each separate uncoated area may not exceed 10 cm?. If uncoated areas are larger, the article containing such areas shall be regalvanized unless otherwise agreed between the purchaser and the galavanizer.
Renovation shall be by zinc thermal spraying or by a suitable zinc rich paint.
The coating thickness of the renovated ares shall be a minimum of 30 ?m more than the local coating thickness requirement.
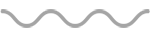